The Advantages of NMT® Titanium Anodes:
- Are environmentally friendly, with the risk of additional toxic or hazardous substances being introduced into the electroplating line being eliminated, eradicating costs that would inevitably arise from the removal of these hazardous substances.
- The inter-electrode gap remains constant throughout the design life of the anode, resulting in the maintenance of a constant voltage and product quality.
- Are Oxygen-evolving with lower anodic operating potentials.
- Once the anodes have reached the end of their design life, the anodes can be cleaned and then re-coated.
- Exhibits a superior catalytic nature, good thermal conductivity, uniform current distribution, high mechanical stability all of which provide superior corrosion resistance.
- Can be used in electroplating of an extensive range of base metals such as copper, nickel, tin, zinc and cadmium as well as silver, gold and platinum group precious metals.
Cathodic Protection Accessories
We can supply numerous accessories for use in CP applications in conjunction with our C anodes, including but not limited to:
- Anode Shields and Housings
- Cables-such as Kynar/HMWPE
- Centralisers and End Weights
- Powerfeed Connectors
Soil Remediation
Our MMO anodes and cathodes can assist in rehabilitating polluted soils. Whether these areas have been affected by inorganic or organic substances, the electrodes are embedded into the contaminated areas and a current applied. The polluting substances migrate to the cathodes and are eventually broken down into hydrogen, oxygen or carbon dioxide.
Hydrogen Fuel Cells
In the ongoing search for energy efficiency and renewable energy, world-wide research hydrogen fuel cells has continued apace. They work like batteries, but do not run down or need recharging, continuing to produce electricity and heat as long as the fuel supply is uninterrupted. A fuel cell consists of two electrodes—a negative electrode (or anode) and a positive electrode (or cathode)—sandwiched around an electrolyte. A fuel, such as hydrogen, is fed to the anode, and air is fed to the cathode. In a hydrogen fuel cell, a catalyst at the anode separates hydrogen molecules into protons and electrons, which take different paths to the cathode. The electrons go through an external circuit, creating a flow of electricity. The protons migrate through the electrolyte to the cathode, where they unite with oxygen and the electrons to produce water and heat. Our anode and cathode products are used as the essential components in the manufacture of Hydrogen Fuel Cells.
Metal Finishing/Electroplating
- Anode performance is critical in realising end-product success in the electroplating industry.
- The use of stainless steel anodes, although relatively inexpensive produce iron oxide (rust) as a by-product of anodic passivation
- The use of graphite anodes results in an increasing inter-electrode gap as the anode dissolves meaning voltage and product quality do not remain constant.
- The use of led anodes, other than being a significant health hazard, would result in the contamination of the finished product. An additional benefit of MMO is the significant reduction of energy required.
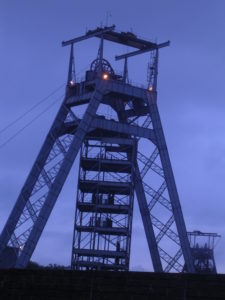
Electro-Galvanising
- Zinc coating of relatively soft metals such as steel and iron not only prevents corrosion but also adds strength to the original uncoated metal.
- Galvanising commonly occurs using the Hot-Dip process where the zinc coating thickness ranges from 1mm – 4 mm.
- The electrolytic process used in Electro-galvanising results in a significantly thinner zinc coat, which is tighter-bonding and with a higher tensile strength than provided by the hot dip method, all at lower cost.
- Our extensive range of anodes are available with a number of coating formulations and loadings which improve the plating uniformity on the coated surface and allow higher plating current densities, all this whilst still reducing energy consumption and operating costs.
Treatment of Ballast Water
The International Maritime Organization (IMO) Ballast Water Management Convention was implemented in September 2019 and all vessels weighing more than 400 gross tons will need to be fitted with a compliant and approved BWTS by September 2024 at the latest. Electrochlorination is the favored method of ballast water treatment, accounting for over a third of all installed systems worldwide (source: DESMI) and uses iridium- and ruthenium-coated electrodes to produce dilute sodium hypochlorite (bleach) in situ. It is projected that between 2019 and 2024, an estimated 40,000 vessels will have to install new ballast water treatment systems (BWTS) to continue operating, supporting demand for iridium- and ruthenium- based electrochlorination systems. Demand for electrodes is forecast to continue through the early 2020s, with year-on-year growth forecast over the longer term as well.
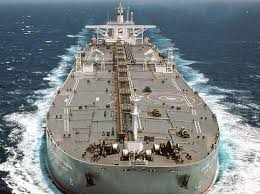